Background
Electrolux, a company specializing in renting out household products like air purifiers and vacuum cleaners, faced significant operational challenges. They had a marketing website where customers could rent these items, but lacked an efficient system to manage the backend logistics. Specifically, they needed a way to track shipments, stock levels in the warehouse, and sync this information with their website.
Previously, they relied on Excel sheets to manage inventory, track rentals, and process returns, but this system was not transparent or capable of providing real-time updates. Furthermore, when items required repair or needed to be sent back after a rental period, the process was disjointed and difficult to manage.
The project goal was to create a centralized CMS system that would seamlessly integrate with the marketing website, provide live updates for both customers and warehouse teams, and streamline the entire rental, shipment, and repair workflow.
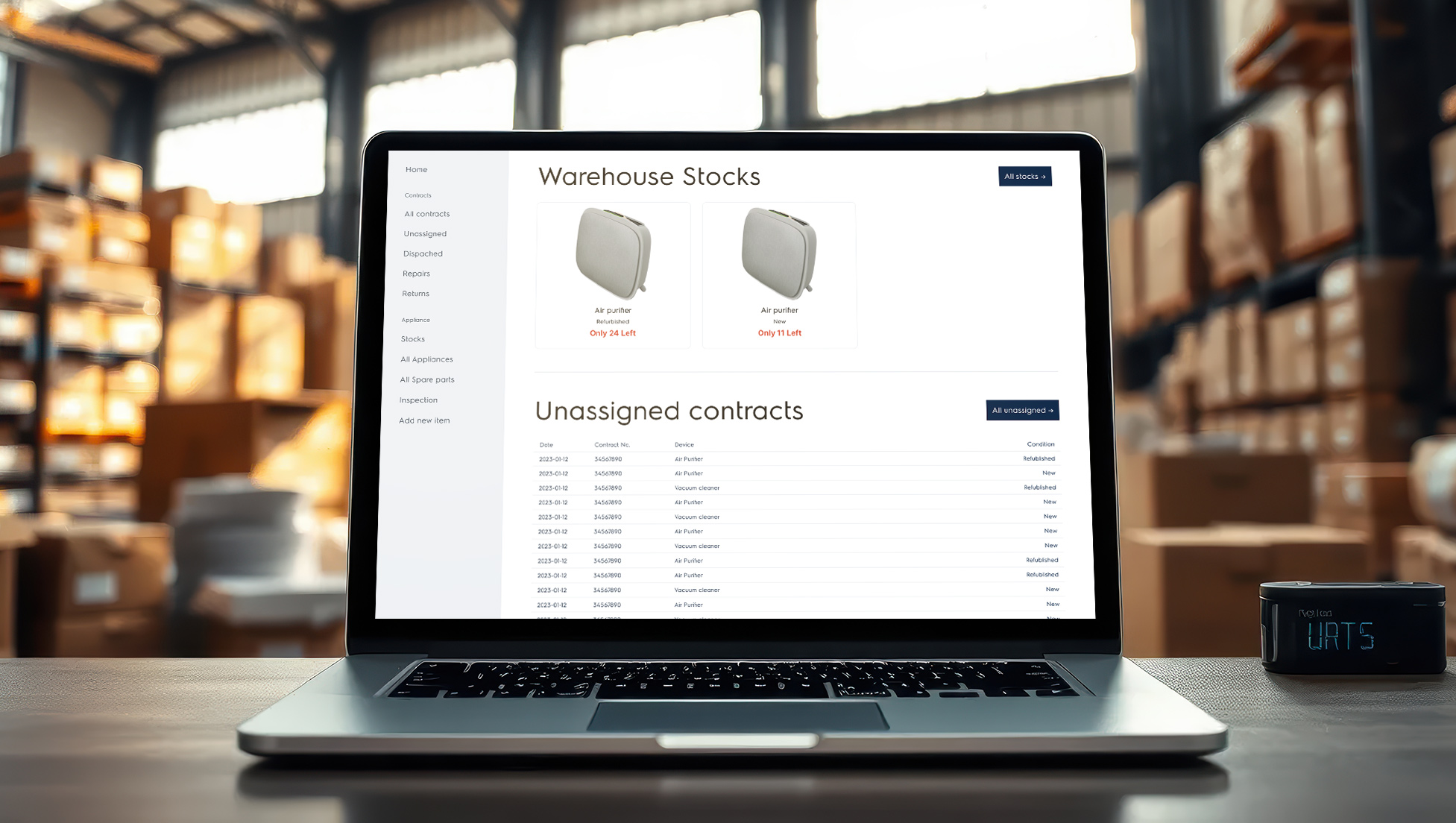
Approach
To kickstart the project, I began by conducting thorough research from multiple perspectives. First, I needed to understand the business requirements and objectives to ensure we were solving the right problems. This involved discussions with key stakeholders to align on the goals and features needed for the system.
Next, I focused on understanding the connection between the marketing website and the backend system. It was crucial to figure out how the marketing website interacted with the system, what data was being passed, and how we could ensure smooth integration between the two. This would allow us to streamline the process and ensure live updates for users when renting and returning products.
Additionally, I conducted research into the operations of the warehouse workers to understand how they were currently managing inventory, shipments, and returns. By learning their workflow, I could better map it to the new system. I created a comprehensive system map that highlighted both the warehouse workers’ perspective and the product flow, ensuring that the CMS was designed to meet both user and operational needs.
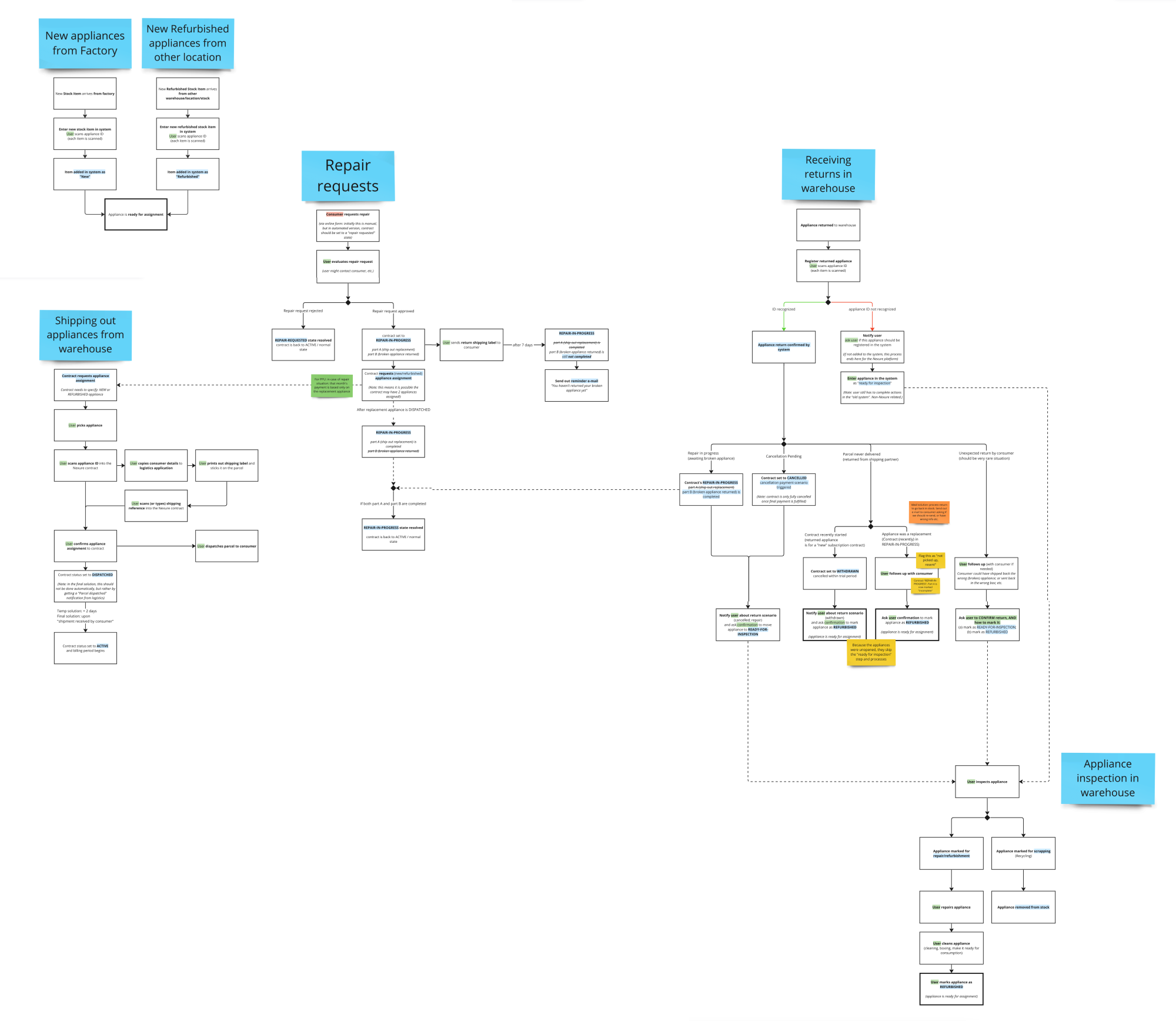
Once I completed the initial research, I focused on creating a design system that would cater to the unique needs of the warehouse environment while still aligning with Electrolux’s broader design principles. Although the system had to align with the Electrolux design system, it needed to be separate to address the specific requirements of warehouse workers. The workers didn’t have the same high-quality screens or ideal lighting conditions as office workers, which required a significant focus on high contrast and legibility.
To meet these needs, I designed an interface with bold contrasts to ensure readability in less-than-ideal lighting environments. The system was simplified to help workers focus on essential tasks, such as managing shipments, checking contracts, and processing returns. The user interface needed to be clear, intuitive, and highly functional, offering a straightforward, easy-to-navigate flow. Additionally, the design had to provide an overview of all critical tasks and statuses, ensuring that workers could carry out their duties quickly and efficiently.
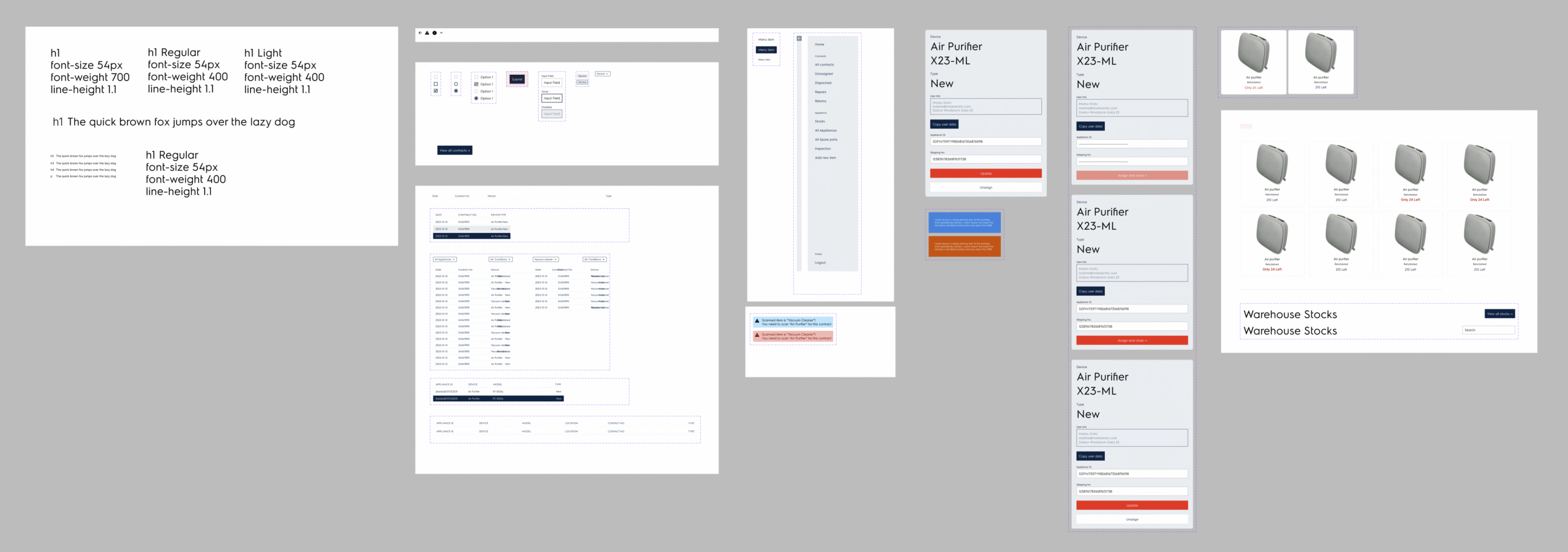
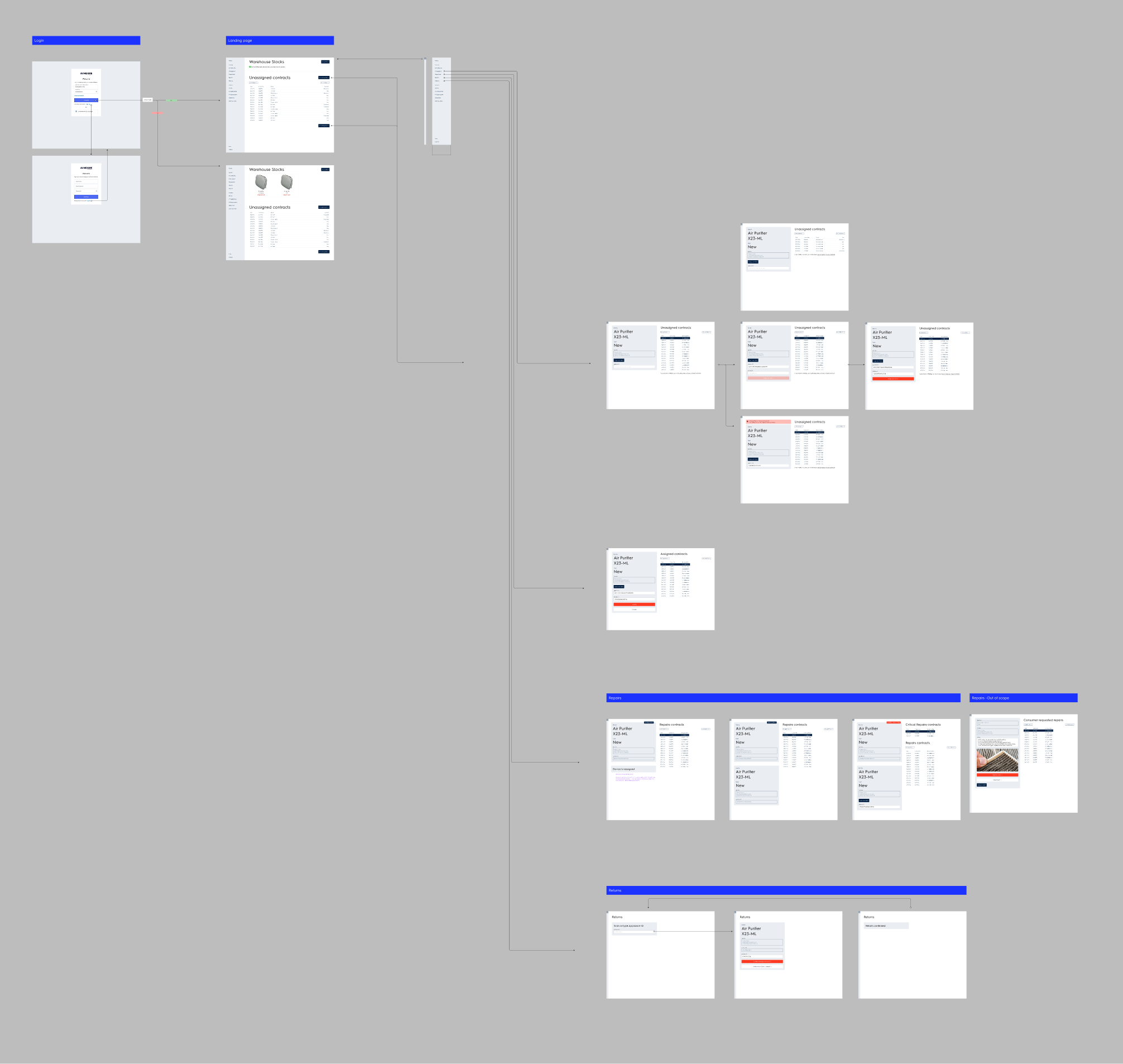
Impact
The project was successfully completed in under two months, and its results were significant. By implementing the new CMS and streamlining the workflow, Electrolux was able to ship products six times faster, vastly improving operational efficiency. The system also provided full transparency across the entire organization, giving real-time updates on stock levels, shipments, and repairs.
Customer satisfaction saw a remarkable improvement, with ratings five times higher than before the system’s implementation. This was largely due to the elimination of delays and misplacements in the shipment process, leading to a smoother and more reliable experience for customers.